How Automated Progress Tracking Improves Transparency on Jobsites and Helps Avoid Rework
September 2, 2021
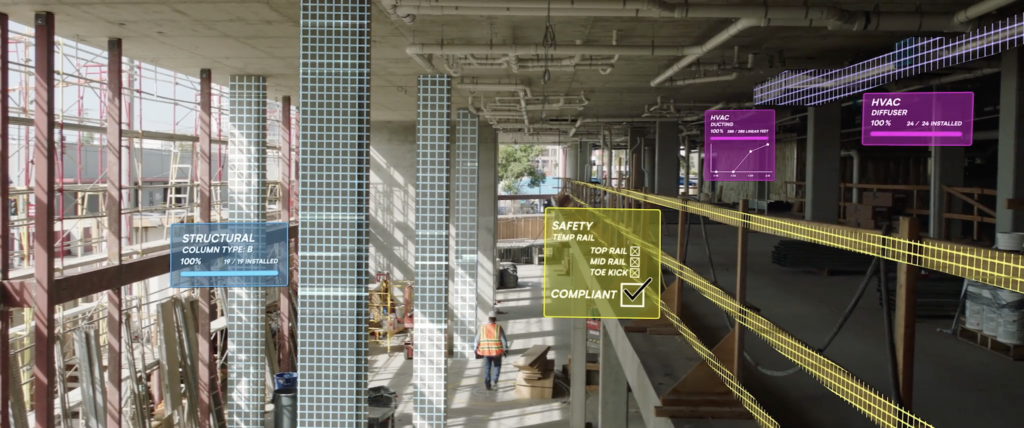
Here’s a primer on how manual construction progress photography is currently used to help GCs, owners, and trades chart the progress of projects—and how AI-powered automated progress tracking is significantly accelerating the pace of construction and improving transparency and communication.
What is progress tracking?
Progress tracking is an effort to provide a reliable record of developments from week to week—or even day to day—to help GCs stay on schedule, analyze team productivity, and keep their costs in check. It also gives owners a view into how projects are progressing—potentially enabling them to start selling units faster and provide WIP evidence for loan draws—while helping trades get paid faster by demonstrating that work is complete. Progress tracking typically starts with construction progress photography, or someone manually taking pictures of each space or room during regular site walks to have a record of progress over time.
What is the current process for construction progress photography?
On most job sites, construction progress photography is handled by Project Engineers or Field Engineers. Armed with an 11×17 inch clipboard and the floor plan, they walk the site and use a highlighter to note the approximate percent of work completed by each subcontractor after performing the calculations in their heads. On bigger projects, the clipboard can have upwards of 30 pages, which makes it cumbersome to work with.
When site walks are complete, the notes are eventually entered into Excel and subsequently uploaded into scheduling software, such as Primavera P6. But this can often take days, which means that any stakeholders who aren’t on-site lack visibility into current conditions.
What is the difference between automated progress tracking and manual construction progress photography?
Automated progress tracking leverages AI to quickly and accurately generate percent complete calculations, quantities installed, rates of work, and estimated completion dates for critical trades across entire projects. This type of automation can be achieved through the use of 360° photo documentation technology to create a detailed record of the project and how it’s changing over time.
When PEs and FEs take construction progress photography with their phones, they’re likely to take only one or two shots of each room per walk, while 360° photo documentation ensures that each room or space is captured from multiple angles. This more complete view of conditions makes it possible for machine-learning algorithms to accurately estimate progress over time.
Compared to automatic progress tracking, manual construction progress photography is highly error-prone, which can lead to inaccuracies in scheduling that disrupt workflow and result in delays. It can also lead to discrepancies with payments and invoices if subcontractors aren’t careful or if the progress record isn’t reliable.
Why does manual construction progress photography lead to scheduling issues?
On a large, complex project, scheduling software like Primavera P6 can contain more than 10,000 individual items, which Superintendents are usually responsible for updating. Sometimes Project Engineers note whether an activity is completed or mark the percentage complete on an iPad during their construction progress photography walks, but in many cases, the estimates are jotted down on paper. Since scheduling relies on proper sequencing and accounting for contingencies, the likelihood of errors grows in proportion to the size and complexity of the project.
Scheduling failures caused by a project tracking approach that relies on manual construction progress photography can lead to many types of disruptions. For starters, if a subcontractor shows up ready to work but the job site isn’t ready for them, they’ll still expect to be paid. (Workers might arrive at the job site expecting to install conduits only to find out that the framing hasn’t been put in yet, for example.) Budgets can spiral out of control due to unforeseen costs of this nature, and then the work that’s completed doesn’t match the budget expenditure.
How does automated progress tracking help with payment verification?
At the beginning of a project, a GC typically accepts bids and chooses subcontractors based on their best estimates of how much work they can do over a certain period of time. The contract usually extends for exactly that amount of time, with the GC paying the trade on a monthly basis. Ideally, the payments should equal about 50% of the total when 50% of the work is completed.
What often happens in practice when progress tracking is manual via construction progress photography is that payments start to outpace the actual percentage of work completed. When the contract period is over, the GC has often paid 100% of the fees when the work is only 80% complete, for example.
Seen from another perspective, no GC wants to be viewed as a “pass-through contractor” who simply passes along subcontractors’ estimates of how much material has been installed to owners without verifying them for accuracy first. But this invariably happens on many construction sites due to the fact that each trade—from drywall installers to electricians to plumbers—is typically free to track what they do in their own way. Project Managers in charge of payment applications are often too stretched to have time to verify each spreadsheet input from every trade, and the owner may overpay significantly as a result.
Automated progress tracking derived from a complete, regularly-updated digital record of the job site can remedy this. If GCs can easily find the discrepancy between the amount of material a trade has recorded as installed and the actual amount installed, they can reconcile it with the trade instead of blindly passing it through to the owner.
How does automated progress tracking increase efficiency?
Automated progress tracking helps project stakeholders across the board. Once the process no longer relies on walking around with a clipboard and highlighter to document the status of specific areas, the Project Engineer clearly benefits in terms of hours freed up to focus on other tasks. (Construction progress photography can be extremely time-consuming.) Project Managers who may have previously spent half their time on payment applications also benefit, since reliable progress tracking means they can check on the status of work from their computer without having to track down the right people to talk to.
At the same time, Superintendents can be more confident about the accuracy of the schedule, while Project Executives and Owners can drop in on the project whenever they want to for a view of actual conditions, unfiltered by what the on-site team wants them to see. Ultimately, automated progress tracking can be the difference between profitable, on-time delivery and significant delays and cost overruns. It provides consistent data that can be used to validate how a delay came to be, rather than enabling unproductive finger-pointing based on someone’s hunch.
How does automated progress tracking improve communication?
The worst mistakes on a job site usually happen because of lapses in communication. Most GCs have robust processes for communicating across teams, including bi-weekly coordination meetings, OAC meetings, the one-week lookahead, and the two-week lookahead, but mistakes can happen even with the best processes in place.
Manual construction progress photography can sometimes lead to slip-ups that have far-reaching consequences. For example, a Project Manager tells their drywaller installer to bring a crew next week to hang drywall on the first floor—without realizing that the top track has yet to be installed and there’s nothing to hang the drywall on. This may lead to a snowball effect where the Project Manager has to reschedule multiple crews, resulting in weeks or even months of delays. These kinds of errors affect the critical path of the project, pushing the timeline for completion out further—in some cases beyond the point of profitability for the GC and/or owner.
This is one of the main reasons top builders are adopting automated progress tracking tools. By maintaining a closer watch on work as it’s completed, GCs are able to avoid costly errors and oversights.
Learn more about automated progress tracking with OpenSpace.