How OpenSpace Progress Tracking Helps Suffolk Increase Transparency and Drive Production Onsite
May 5, 2021
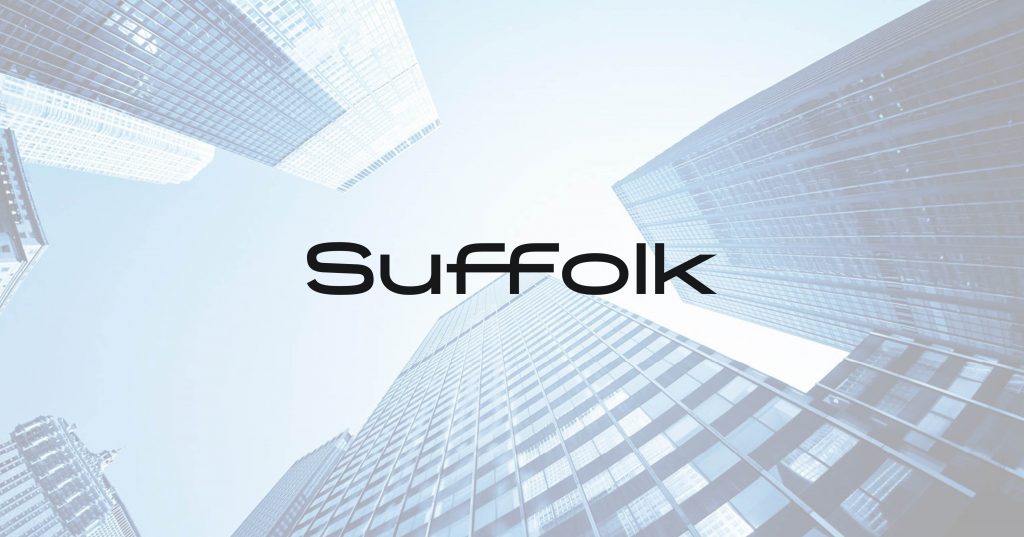
Suffolk Construction’s innovative technology piloting program identified OpenSpace as a high-impact construction solution after evaluating the platform’s usability and value proposition in 2019.
With a solid foundation in using OpenSpace, Suffolk became interested in leveraging the documentation for improving an existing onsite process: progress tracking.
Accurate progress tracking of specific materials has many potential use cases on a job site, such as lean planning, flow and material management, verification of work, and much more. Typically, team members meticulously walk the site with a set of plans and a clipboard, estimating progress visually and recording percent complete. Automating this process with accurate data capture would prove to be a gamechanger.
Suffolk began using OpenSpace’s OpenSpace Track automated progress tracking product on its Estates at Acqualina project in Sunny Isles Beach, Florida, which consists of two 827,000-square-foot luxury towers. The progress tracking module ingests captured imagery from day to day and compares the documentation to produce accurate percent complete values for drywall, framing, insulation, and sheetrock. (For the Acqualina pilot, Suffolk has primarily been utilizing the tech for drywall installation tracking.)
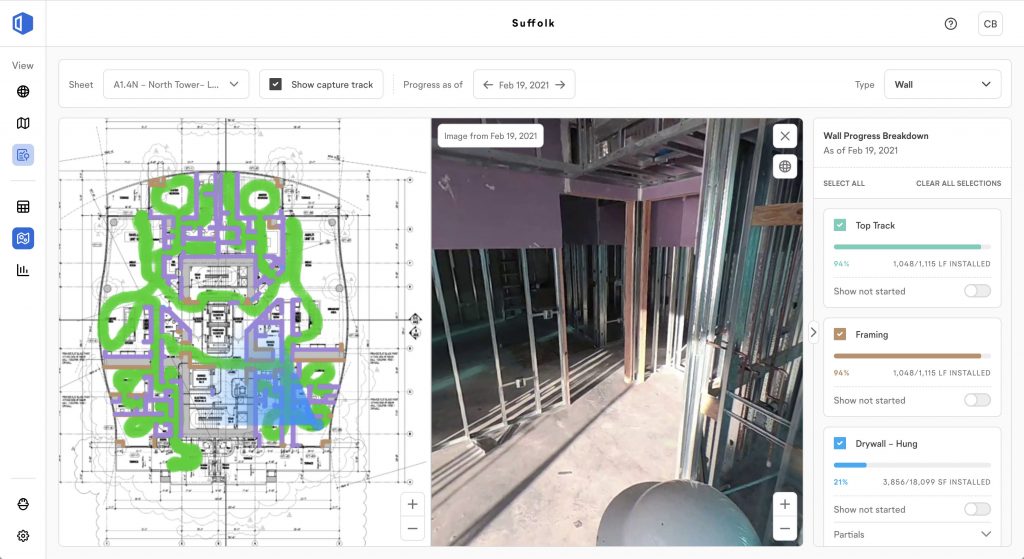
Suffolk has been leveraging lean scheduling and planning for years, but tracking accurate work-in-place values has been a challenge. OpenSpace’s progress tracking capabilities have been highly useful in understanding the current Planned Percent Complete (PPC) of each trade partner (i.e., how each trade is currently tracking against their “promises” or commitments for that week). With highly reliable work-in-place values, the field team can adjust variables, such as manpower. If a specific trade were noted as falling behind the weekly work plan, they could be notified and supported to make up for the lost time. This allows for quick course-correction onsite and ultimately drives production.
In addition to increased transparency onsite and reliable work-in-place tracking, Suffolk anticipates that automation will yield significant time savings. For example, after recently getting a bill for masonry work, Project Engineer Javier Contreras had to visit the area with the trade partner and verify the installation of work by literally counting the units of material—of which there were roughly 50,000. With automated progress tracking, verifying the percent complete would be instant.
“It would have saved a whole day of work,” Contreras said.
OpenSpace also provides a clear insight into the quality of the work in place and makes it much easier to assign outstanding work to trades. For example, the Acqualina project features very high-end condo units, which require the utmost attention to detail. With OpenSpace’s Field Notes feature, it’s easy to take pictures of defects and have them automatically mapped to the floor plan and flagged to relevant trades for instant notification and rework. It’s also possible to identify housekeeping issues faster and clearly direct the responsible party to clean them up.
To learn more about how Suffolk Construction is using OpenSpace for quality control and to increase transparency with owners and design team members, download the case study.