How Power Design Uses OpenSpace to Enhance Productivity and Future-Proof Operations
Power Design, Inc. is a design-build contractor based in St. Petersburg, Florida that works across multiple trades, including electrical, mechanical, plumbing, and systems technology. The company brings its expertise to residential, assisted living, hospitality, and mixed-use projects across the U.S.
Power Design was looking for a documentation solution that would help the business scale sustainably and maximize efficiency—without creating extra work for field teams. The contractor selected OpenSpace’s reality capture solution to standardize operations and foster collaboration and soon deployed the technology company-wide after piloting it at three locations.
Read this case study to learn how, working with OpenSpace, Power Design has achieved significant time and cost savings, improved productivity, expedited issue resolution, and future-proofed its operations.
Learn more about the products and technologies featured in this case study:
- Video: Why Power Design Selected OpenSpace
- Webinar: Power Design’s Best Practices for Using OpenSpace
- OpenSpace Capture
- Save Time and Money with 360° Reality Capture
Melvin Gonzalez
Director of Field Technology
Power Design, Inc.
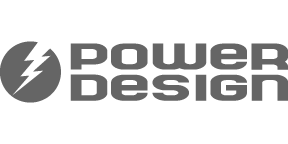