How CEC Uses OpenSpace to Improve Communication with General Contractors
CEC Facilities Group is one of the fastest-growing, top-ranked specialty subcontractors in Texas, serving clients in Texas and throughout the U.S. CEC offers complete electrical, mechanical, plumbing, technology, A/V, service, and installation solutions.
CEC came to OpenSpace with the goal of improving photo documentation for conversations with GCs. CEC team members frequently need to show accurate job site conditions before starting work. Having thorough, easy-to-navigate photo documentation to quickly show GCs true site conditions became a high priority. The team also needed to ensure rapid adoption of the technology and demonstrate its value quickly, so ease of use was high on the priority list when the company was evaluating solutions.
Read this case study to learn how, working with OpenSpace, CEC has significantly reduced time spent documenting jobsites, improved issue resolution and communication, and secured high levels of platform adoption.
Jared Peinado
Director of Project Controls
CEC
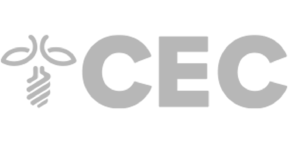