How U.S. Engineering Uses OpenSpace to Mitigate Risk and Reduce Travel Time
Founded in 1893, U.S. Engineering is a full-service mechanical contractor serving the Midwest and Rocky Mountain regions. The firm is routinely ranked in the country’s top 20 mechanical contractors and top 100 specialty contractors by ENR.
U.S. Engineering was looking for a more thorough way of documenting job sites and turned to OpenSpace. The company soon found new ways to leverage OpenSpace throughout the organization as word spread about the technology, leading to large time savings, risk reduction, avoidance of costly rework, increased transparency with owners, and improved accountability among project stakeholders.
Read the case study to see how OpenSpace’s BIM Viewer, Field Notes, OpenSpace Track progress tracking, and 3D Scan tools work together and how these technologies can unlock significant, measurable results for your business.
Learn more about the products and technologies featured in this case study:
Chad Lucks
Quality Control Manager
U.S. Engineering
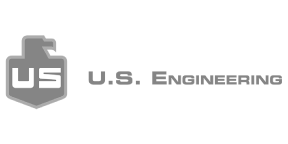