How Tishman Speyer Uses OpenSpace to Strengthen Tenant Relationships and Improve Communication
Tishman Speyer is a leading owner, developer, operator, and fund manager of first-class real estate across the globe. Founded in 1978, many of the world’s most prestigious corporations rely on Tishman Speyer to meet their space needs.
Tishman Speyer was looking for cutting-edge technology to help improve delivery and operational efficiency, and the company noted OpenSpace’s potential to improve numerous processes and workflows by letting field teams seamlessly capture 360° imagery. Moreover, teams could now see through walls and capture the state of the framing, electrical, plumbing, rebar and more for posterity. This new-found “X-ray vision” has also prevented costly rework and minimized disruption to existing tenants by helping teams pinpoint where to focus instead of opening up large sections of wall.
Read this case study to learn how, working with OpenSpace, Tishman Speyer is benefiting from having a single source of truth with smoother hand-offs, improved stakeholder communications, significant time savings in the field, better collaboration, and avoidance of costly rework.
Learn more about the products and technologies featured in this case study:
Eleftherios Pittas
Senior Director of Design and Construction
Tishman Speyer
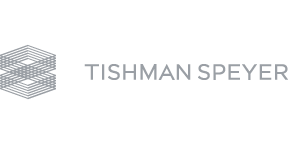