How The Boldt Company Uses OpenSpace to Keep Healthcare Projects on Schedule
Founded in 1889, The Boldt Company is a leading construction management firm in the United States. The company is a nationally recognized leader in Integrated Lean Project Delivery® within a variety of markets including healthcare, industrial, commercial, and energy and power.
Healthcare construction projects have specific safety protocols and unique design challenges that add layers of complexity. Boldt sought a solution that offered more robust photo documentation and could help make numerous workflows and processes more efficient. The firm chose OpenSpace to increase transparency across stakeholder groups and improve coordination on its most complex healthcare projects.
Read this case study to learn how, working with OpenSpace, Boldt has had 20% fewer scheduling delays, saved hundreds of hours on coordination, and secured 100x more complete documentation over its prior manual processes. The company has also seen more efficient resource allocation, reduced rework, and significant cost and time savings.
Aaron Frederick
Senior Project Manager
trade partner Martin Petersen Co.
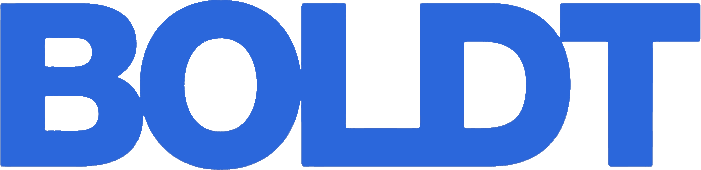