Namibia Construction is one of the most successful construction companies in Namibia. With 72 years of experience, the company focuses on delivering top-quality projects, from building construction to civil works, roads, mining, and more—all within the borders of Namibia.
The challenge
In 2023, the company completed the construction of the Mokuti Etosha lodge. It is situated at the gates of Etosha National Park, 105 kilometers away from the nearest town and over 500 kilometers away from the Namibia Construction headquarters in Windhoek.
The remote location represented a huge logistical challenge for the team, but that wasn’t the only one. The luxurious lodge had to be completed with the highest quality standards within a very ambitious time frame, all while facing a challenging skilled labour market. As Du Bois Louw, Quantity Surveyor at Namibia Construction, puts it, “From the get-go, we had to do more with less time and therefore expect more from each colleague, also on the management level.”
Even though a QA process was already in place, the existing manual method of capturing photos and writing diary entries would not allow the team to manage the day-to-day work of the project remotely. “There’s always that one photo in a specific location that you need, but you didn’t take”, says Du Bois. For him and his team, this is the biggest frustration with a manual documentation process—wasting valuable time trying to find a specific photo after the fact. “Pre-OpenSpace, the time it took to filter through hundreds of photos was significant. Finding photographs took a whole week on a previous project where we had to resolve an issue.”
When Du Bois and a colleague first saw a demonstration of OpenSpace at a local conference, they immediately put together a business case to secure investment for the 360° reality capture solution. Their proposal: With OpenSpace, senior management could reduce travel to and from the project site significantly. The travel cost saved was directly invested into using OpenSpace. “In the end, we were even better off with OpenSpace. We got more value than what we’ve spent”, says Du Bois.
The solution
The same Quality Control Agent that previously had to go from room to room to take photos is now walking the site with a 360° camera and the OpenSpace mobile app on a daily basis. “With OpenSpace, documentation is much faster, because you can just continuously walk through the site”, says Du Bois. No more stopping in every room to take dozens of individual photos. There is also less reliance on the QC Agent to know what photos to take. As Du Bois puts it: “With OpenSpace, he might not even see the issue, but it’s still documented.”
Thanks to the daily captures, Du Bois and his team can now access the project site any time and from anywhere. During coordination meetings in the Namibia Construction offices, all key stakeholders, including subcontractors, architects, and engineers, come together to review site progress in OpenSpace and discuss current issues. “If we want to discuss an issue in the pool bar, we just physically jump to that point in OpenSpace”, says Du Bois.
When on-site with consultants and key stakeholders, we now look at three key items and fix them instead of having to look at 20 items and not one is solved at the end of the day.
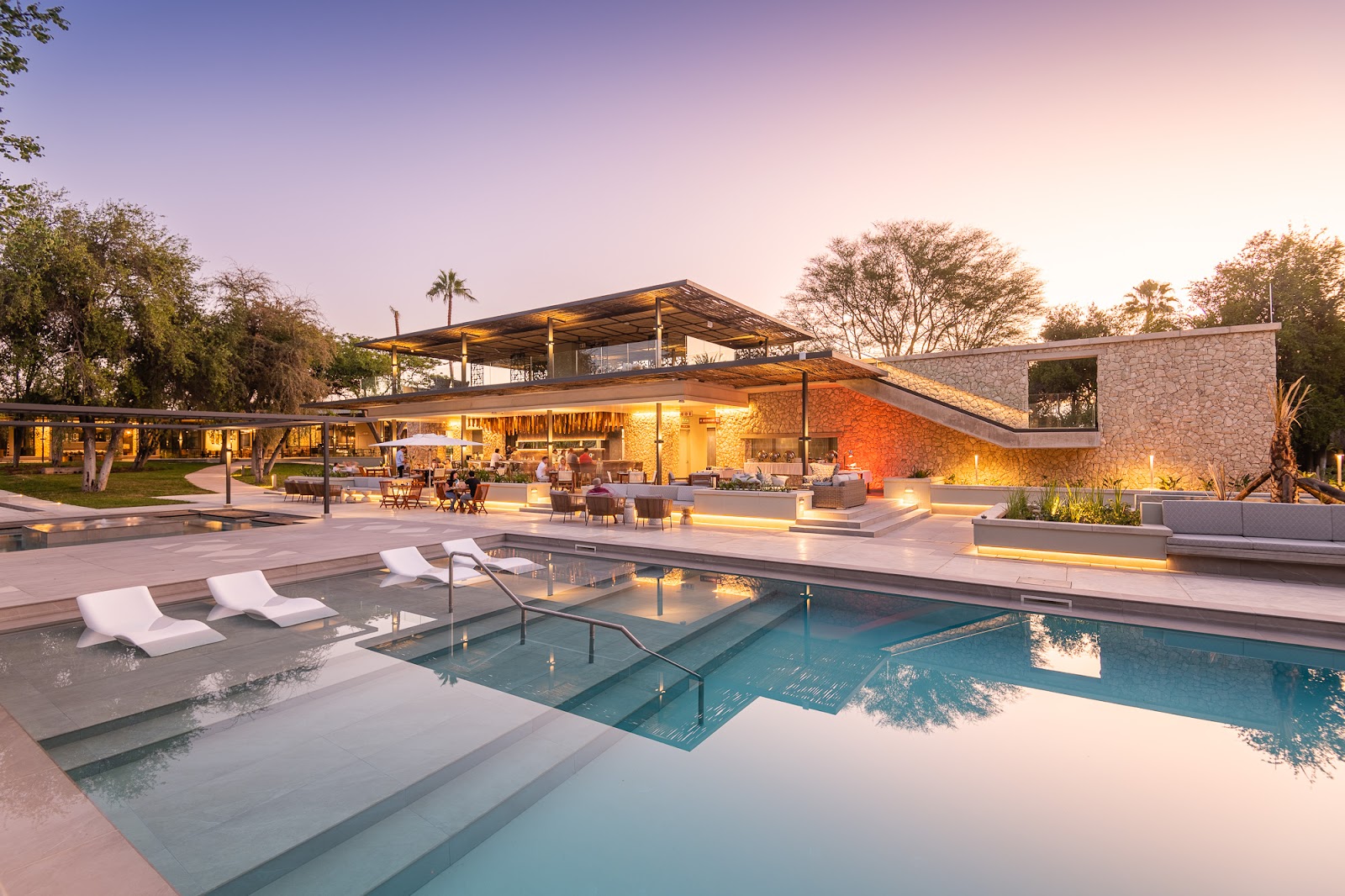
The results
The team was able to cut site travel in half, saving the company not only a lot of money but also valuable time that can now be spent on more pressing project management issues. Plus, the site visits that do happen have become a lot more focussed and effective. “When on-site with consultants and key stakeholders, we now look at three key items and fix them instead of having to look at 20 items and not one is solved at the end of the day”, Du Bois says.
Daily captures with date, time and location
Having daily captures of the construction site marked with the relevant date, time, and location has also been a huge help in resolving and even avoiding disputes. In the past, issues on site often led to finger pointing.
Now OpenSpace provides clear and objective proof of what happened on-site and when. Everything is documented so everyone is accountable. According to Du Bois, this has set the tone for the project and has greatly improved how stakeholders cooperate and communicate with each other.
For the Mokuti project, Namibia Construction had access to a 3D model that the project consultant created. The model was uploaded to OpenSpace and, thanks to the BIM Compare feature in OpenSpace Capture, the team was able to compare the model side by side with the as-built reality. The result: Potential issues were detected before they became problems. “I can’t even put a number on how much value OpenSpace has created for us just by saving unnecessary rework”, Du Bois says.
Getting the team started with OpenSpace was quick and easy according to Du Bois. “One of the foremen was skeptical at first, but then he ended up needing OpenSpace to complete a tricky part of the project and he was really happy to have the captures available”, he says. The problem? The team kept hitting water pipes when installing their work. So the team used the Split View feature in OpenSpace Capture to look behind the already closed-up wall and avoid any further damage.
Given the huge success at the Mokuti project, Namibia Construction is planning to roll out OpenSpace further across the business. To Du Bois and his team, their investment has clearly paid off and the value became clear very quickly. It’s not just a tool to help them build better and more efficiently but also an added value the company can offer to existing and future clients.