The challenge
Building and renovating hospitals is detail-oriented work that requires close coordination with qualified trade partners to ensure that installation is done correctly and sites are kept clean. Each room needs to have a variety of ports for oxygen, nitrous and vacuum lines, and MEP infrastructure is significantly more complex.
With 60% of its work in the healthcare sector, Kitchell was looking for ways to reduce risk and be a more efficient partner to its stakeholders. The Phoenix-based company also wanted to improve its handoff process with hospital facilities departments, which usually aren’t involved in construction and are often left flying blind when issues arise (since they have no idea what’s behind the sheetrock or under the concrete).
The solution
Knowing that more robust documentation would improve a number of processes, Kitchell’s Field Engineer Jeff Manders tested OpenSpace along with two competing photo documentation solutions, StructionSite and Matterport. He found that OpenSpace’s ability to capture images automatically and map it to floor plans was a huge differentiator. One of the other solutions let him take still 360 photos and manually tag them on the floor plan, but the process was slow and documentation coverage was sparse in comparison.
Since then, Manders and his teammates have deployed OpenSpace extensively on a 750,000-square-foot tower for a healthcare system. (He’s captured 3 million square feet personally in the last six months.) Since OpenSpace integrates seamlessly with Procore, it was simple to attach captured imagery to RFIs, QA items, and safety observations.
Another early use case Manders discovered was showing OpenSpace captures at weekly meetings with trade partners and daily huddles with foremen to communicate upcoming work, site logistics and even housekeeping. He used OpenSpace’s Object Search feature to identify piles of trash around the site and show them to the trades responsible for cleaning up.
“It’s just easier to hop around the site on OpenSpace so that everyone can see what I’m talking about,” he said.
Manders is also an avid user of OpenSpace’s BIM Viewer feature, which enables a side by side view of current site conditions with the model; it helps him catch discrepancies that require RFIs. For example, BIM Viewer enabled him to identify a missed stub-up prior to pouring concrete. This could also have been achieved by bringing up the BIM model on an iPad, but someone would have needed to be on-site at the right location to see if the installation matched the model. With OpenSpace, this type of check can be done anywhere.
Kitchell recently entered into an enterprise agreement with OpenSpace and plans to implement it on all projects going forward, including non-healthcare projects.
OpenSpace isn’t just a documentation tool, and that’s why we’re so excited about it. It touches so many different workflows.
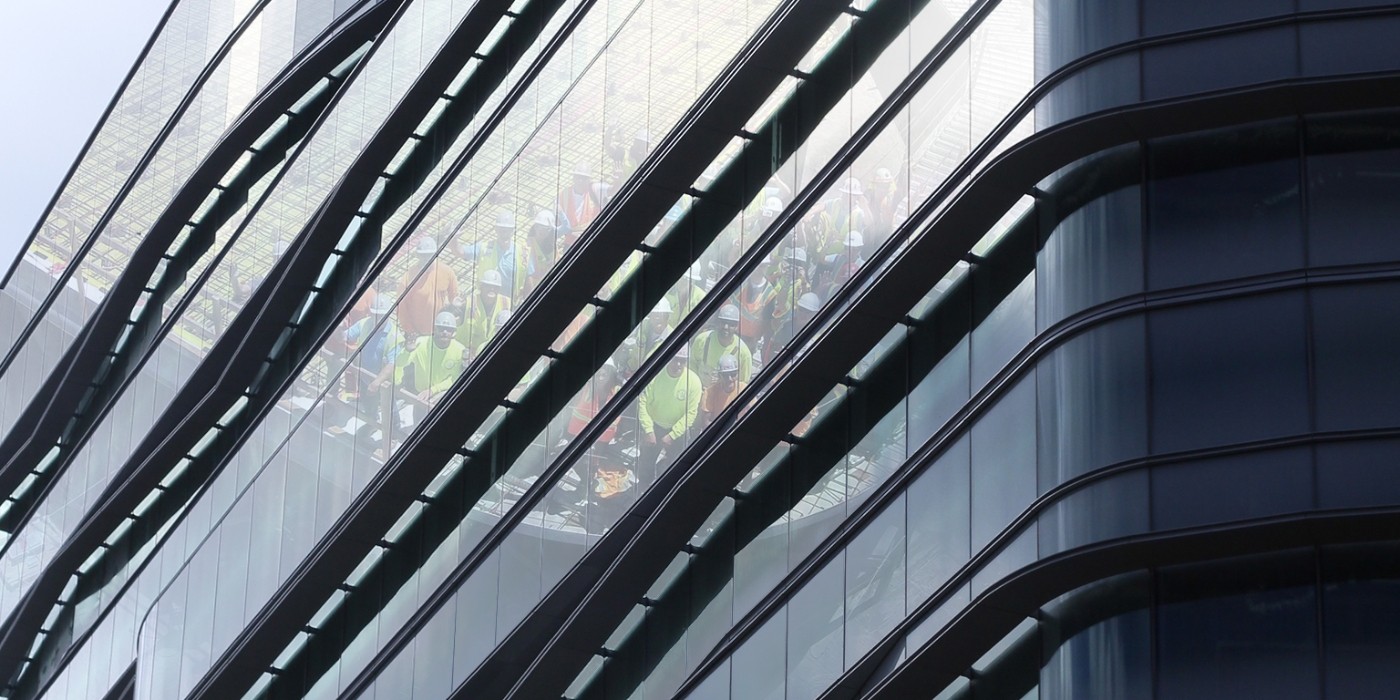
The results
“OpenSpace isn’t just a documentation tool, and that’s why we’re so excited about it,” said Mike Fitch, a Project Director who’s part of a team charged with improving operational excellence at Kitchell through cutting-edge technology. “It touches so many different workflows.”
10X faster
Tens of thousands of dollars
Kitchell has already seen strong results in the following areas:
Savings on rework
Though Kitchell is at an early stage of its company-wide rollout of OpenSpace, there are already examples of the technology helping to avoid rework, such as an RFI that required pinpointing the location of an in-wall reinforcement to determine how best to resolve the issue. One resolution required higher cost, coordination and labor than the other. By referencing an OpenSpace capture from before the reinforcement was covered, the cheaper—and safer—of the two solutions was selected. Fitch also points to a previous project where the company would have saved $30,000 to $40,000 had OpenSpace been available. Kitchell
had built recreation fields for a university, and fencing was added to the scope at a relatively late stage. Since the project team didn’t have thorough documentation of the irrigation lines during installation, they had to do time-consuming manual pot-holing to avoid clipping the lines with a drill.
More transparency internally and with owners
OpenSpace is enabling owner representatives, architects and designers to track progress without visiting sites in-person. This has been especially valuable in the pandemic, since projects like the new tower are active hospitals that treat COVID-19 patients. “Owners and our senior leadership can validate that on-site teams are where they say they are in the schedule and have a bright, clean jobsite,” Fitch said.
Improved handoff to facilities teams
Before having OpenSpace, Kitchell teams would have spent hundreds of hours organizing still digital photos that had been taken throughout the project in order to organize them in a usable format for end users. With OpenSpace, they can provide captures that show the pre-sheetrock and pre-concrete pour state of the building, which are mapped to the exact location in the project on a floor or site plan. This gives facilities teams a view of what’s behind walls, making it easier to proceed if they need to install new Cat 6 lines or new equipment supports, for example. “OpenSpace is a living document of everything that’s running behind the sheetrock and under the concrete,” Fitch said.
More efficiency in pursuits
Kitchell is ramping up usage of OpenSpace for pursuits. Instead of taking manual photos during pre-bid walks, the pre- construction department can use the technology to more fully capture a location, which makes logistics planning and budgeting easier.