Between capturing, organizing and searching through images over the lifespan of a project, it’s no secret that project teams have long desired a faster and more efficient process to document, view and track jobsite progression.
A critical component of documenting Balfour Beatty’s work throughout the construction process, jobsite capture assists project teams with quality control and inspections, helps identify safety hazards and can even be leveraged as a point of reference following project completion. This process might not seem complicated, but it can amount to a considerable investment of time and resources when capturing and cataloguing thousands of images over the lifespan of a project.
Eager to identify an innovative solution that improved the efficiency and effectiveness of jobsite capture, Balfour Beatty’s construction technology team began testing and implementing OpenSpace, a cutting-edge, cloud- based software that has revolutionized how project teams capture, organize and store images throughout the lifespan of a project.
In advance of the accelerated digital transformation brought about by COVID-19, Balfour Beatty delivered this solution to project teams across the nation, which among other operational benefits, enabled remote team members and clients to observe real-time jobsite progress.
The challenge
Before leveraging OpenSpace technology, Balfour Beatty teams utilized platforms that required a teammate to manually mount a 360° camera on a tripod, capture progress photos and pin those photos to the correct building location—repeating this tedious and time- consuming process in multiple jobsite zones.
Balfour Beatty’s industry-leading technology experts knew there had to be a faster and more efficient method that would create more value for their clients and partners. The answer? OpenSpace.
The solution
Through the use of a 360° hard-hat mounted camera, this innovative software enables a faster and safer handsfree jobsite walk, giving project teams greater agility. It also saves valuable production time by eliminating the action of pinning each photo with its associated location. Instead, the person walking the jobsite tells the program where they are on the plans at the beginning of the capture. As they walk the jobsite, the OpenSpace software utilizes simultaneous location and mapping (SLAM), a technique that constructs a map of an unknown environment while simultaneously moving through it and estimating the path of the walker on a floor plan while taking a rapid two photos per second—a frequency that increases Balfour Beatty’s capture rate by roughly 75 times from the previous platform. The captures are then fed into a machine learning system that refines the estimate and increases accuracy with every walk.
Our project teams have reaped great benefits, resolved countless issues, and saved time and money for the business, trade partners, and clients.
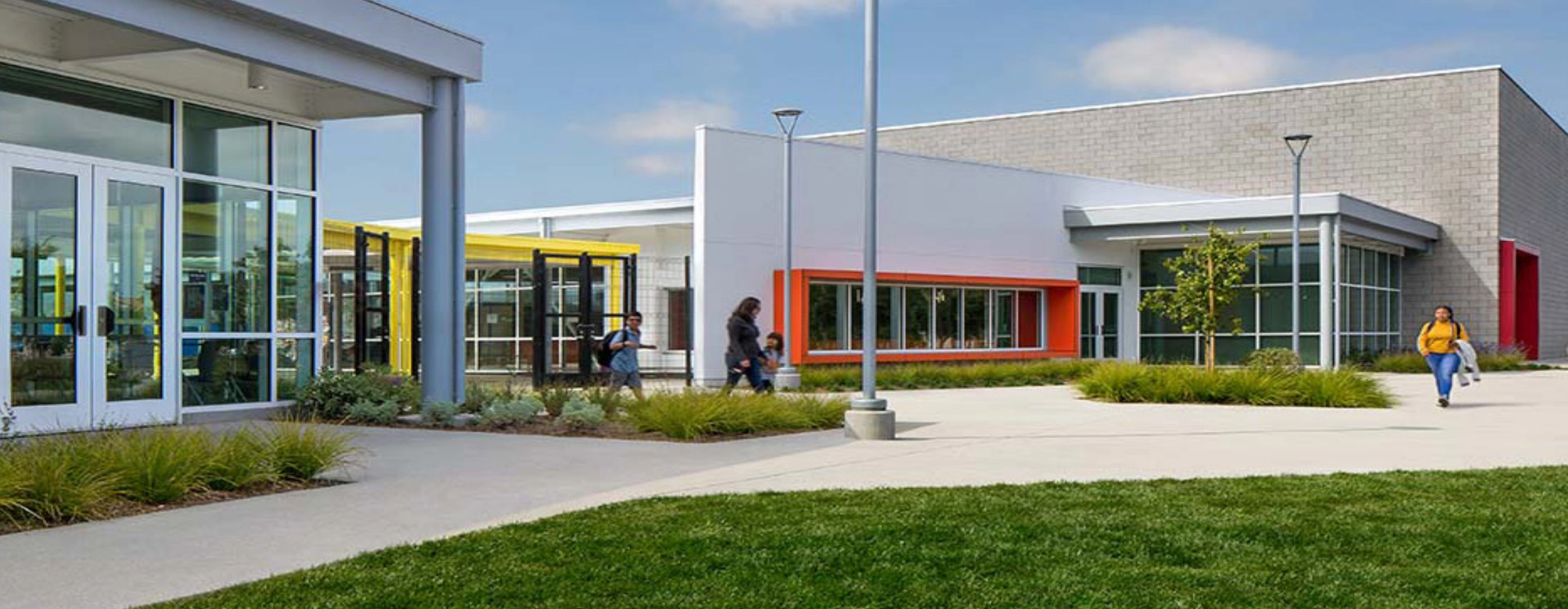
The results
And the time saved undoubtedly speaks for itself. Prior to implementing OpenSpace, Balfour Beatty’s Texas Buildings team captured 2,135 images during 71.96 hours over five months on the EPIC 2 project. But, after implementing the software on another project, JP Morgan Chase interior finish out, they captured over 160,474 images in approximately 22.29 hours over the same five-month span. As anyone in construction knows, more frequent documentation provides better tracking of jobsite progress, saving valuable time and money for project teams and clients alike.
When our project team used OpenSpace consistently throughout the jobsite, it proved to be an invaluable tool.
“We experienced multiple instances where the project team benefitted from the vast amount of data collected from the walk-throughs. Due to COVID-19, many of our stakeholders and representatives not located in DFW were unable to travel. OpenSpace allowed the project team to quickly provide real-time updates and walk-throughs, further providing stakeholders the opportunity to review progress, track quality control and review various inspections. Our project management team also utilized the program for schedule updates, quality control documentation, in-wall inspections, audit reviews and subcontractor billings, among other benefits. These tasks would have been near impossible with the previously used platform.”
OpenSpace also utilizes interactive and artificial intelligence (AI) tools that enable Balfour Beatty’s teams to perform documentation and critical communication tasks throughout the project. These tasks include comparing work put in place with a coordinated Building Information Modeling (BIM) model, checking the placement of sleeves and penetrations before concrete pours to coordinated locations, converting field notes into BIM 360 issues and assigning responsible parties to execute any relevant change orders.
It also allows teams to conduct virtual safety walks and provides often needed historical side-by-sides, all stored in one organized cloud space location, preventing the once cumbersome process of searching through overloaded network folders and eliminating the possibility of lost documentation. By leveraging OpenSpace, project teams can also track which team members are conducting the photo capture, and more importantly, how much time and associated investment they are spending doing so.
“In my experience, it can take upwards of 30 minutes to locate a relevant photo of the area behind a visual impediment in a file filled with thousands of other photographs,” says Mikayla Socia, Balfour Beatty assistant superintendent in California. “OpenSpace makes finding several relevant pictures for any location at any point in time on the jobsite a quick and seamless process. We recently had a small water leak coming out of a wall at the County of San Diego Juvenile Justice Campus. By referencing OpenSpace to determine what utilities were in the wall and how they were run, we pinpointed exactly where to open the drywall and fixed the issue quickly with minimal drywall replacement. Without that picture to immediately assist in locating the leak, our team could have experienced extensive and costly rework.”
Leveraging OpenSpace across the business
One of the most beneficial features of OpenSpace is its progress tracking function used to detect changes from one capture to the next for framing and drywall work. Photo documentation through OpenSpace has saved project teams valuable time and money by preventing or minimizing re-work. If an issue does arise, project teams can resolve the situation faster, potentially avoiding an expensive and time-consuming demolition to stay on track with the project schedule and budget.
At North Carolina A&T State University’s Engineering Research and Innovation Complex (ERIC), a state-of-the-art interdisciplinary and multi-functional facility, OpenSpace empowered the project team to troubleshoot potential in-wall issues including blocking, telecom boxes and light switches. By utilizing OpenSpace, the team rapidly identified relevant images that enabled trade partners to install blocking and fix junction boxes and light switches in the necessary locations, ultimately preventing time-consuming and potentially costly re-work.
For a project of this magnitude, the manual capture of in- wall photos alone would have taken a team member up to two days, and even then, it might have been possible to miss key areas. But with OpenSpace, teammates were able to eliminate that process and ultimately able to efficiently capture the entire project from start to finish.
But those were not the only benefits at ERIC; the project team also used the software to compare actual site conditions with a coordinated model, which led to quick resolutions amongst mechanical, electrical and plumbing trade partners – a win for all stakeholders across the board.
In the past, photo documentation was never as strong as it could be, and most teams did not capture progress with enough frequency and detail to accurately show the status of the project from day-to-day. Our project teams have reaped great benefits, resolved countless issues and saved time and money for the business, trade partners and clients.
At the Harnett County Resource Center and Library in Lillington, North Carolina, the project team encountered numerous power/data receptacles as well as other wall- mounted devices that needed to be relocated due to clashes with casework. Although some conflicts were identified during the rough-in phase, the project team subsequently discovered several locations after rough- in that required changes. Using OpenSpace to reference what was previously installed within the walls allowed the project team to identify the existing pathways, which in turn reduced the extent of the work, kept costs down and the project on schedule.
In Fort Lauderdale, Florida, the project team at Broward County Convention Center West Expansion utilized OpenSpace to compare penetrations to the model before the concrete pour. The team would walk the deck prior to the pour to capture the sleeves placed by trade partners. This allowed the team to see a direct side-by-side comparison of the coordinated model and with real-world conditions. This also allowed the team to locate a sleeve that had been placed incorrectly that could have resulted in schedule delays if discovered after the pour.
Innovative technology provides efficient project delivery
As an industry leader, Balfour Beatty seeks innovative and custom solutions to continue to advance business initiatives, streamline operations and enhance services to their clients. Balfour Beatty’s use of OpenSpace has revolutionized jobsite capture and the use of project data both during and after construction.