KEO International Consultants is a highly integrated and agile creative AEP/PMCM (Architectural, Engineering, and Planning / Project and Construction Management) enterprise where innovation is a way of life. KEO’s core values of agility, empathy, advocacy, pragmatism, dedication and integrity guide the expertise of its 2,600+ perceptive problem solvers who help clients shorten the distance between inspiration and realization. Highly talented multinational professionals operate across two continents in 10 offices, contributing to many iconic projects in the Middle East, such as the Louvre in Abu Dhabi, the Lusail Stadium in Qatar and multiple giga-projects in Saudi Arabia.
The challenge
In 2023 KEO was approached to support with the PMCM of a set of projects, covering Mixed Use & Residential Buildings in Historic Diriyah. One part of the project involved a car park with five underground storeys spanning more than 75,000 square meters.
When KEO took over, their goal was to improve stakeholder alignment and cross-team collaboration to ultimately accelerate the project timeline and ensure a smooth handover of the project.
The solution
To quickly get a complete overview of the project, its status and underlying issues, James Golland, KEO Project Director decided to implement 360° reality capture with OpenSpace. By simply walking the construction site with a 360° camera attached to a hard hat, the field team was able to capture the entire project. The result was a complete visual record of the car park, giving the client and all involved stakeholders remote access to the project and a clear understanding of its status.
In order to monitor progress, the field teams continued to use OpenSpace to capture the site on a weekly basis. This ensured that project leads were on top of latest developments and had the right data to delegate tasks to their team members.
To mark up any observations or issues, the teams were using the OpenSpace Field Notes functionality. Whether it’s a Supervision Lead Engineer marking up discrepancies in the as-built against approved drawings or a general issue, a Health and Safety lead flagging a safety hazard or an architect flagging design changes–the relevant person can simply add a new Field Note by clicking on the relevant area in the capture. Every Field Note gets automatically pinned to the floorplan and creators can add descriptions, choose a priority or category for the field note, assign users or add due dates. This way whoever is in charge of resolving the issue knows exactly where to go and what to do.
The team also used additional tools to centralize communication and facilitate project management. Relevant processes were set up to ensure an optimal synergy between OpenSpace and those tools. Aconex for example provided a centralized platform for document management, communication, and collaboration, while OpenSpace facilitated real-time collaboration and communication across all stakeholders. The project schedule on the other hand was developed and managed using Primavera P6, a comprehensive project management software. OpenSpace enabled the team to compare site progress against the P6 schedule with timestamp records.
The captures also served as a proof of completed tasks, such as the deep cleaning of epoxy floors, and ultimately readiness for handover. This also allowed the team to leverage OpenSpace for project cost management, facilitating contractor interim payment applications, review and authorization on a monthly basis. Specifically, OpenSpace helped the team compare contractor claims against materials on site and completed works, providing a detailed, floor-by-floor analysis.
OpenSpace provided us with unparalleled access to real-time, visual documentation of the project.
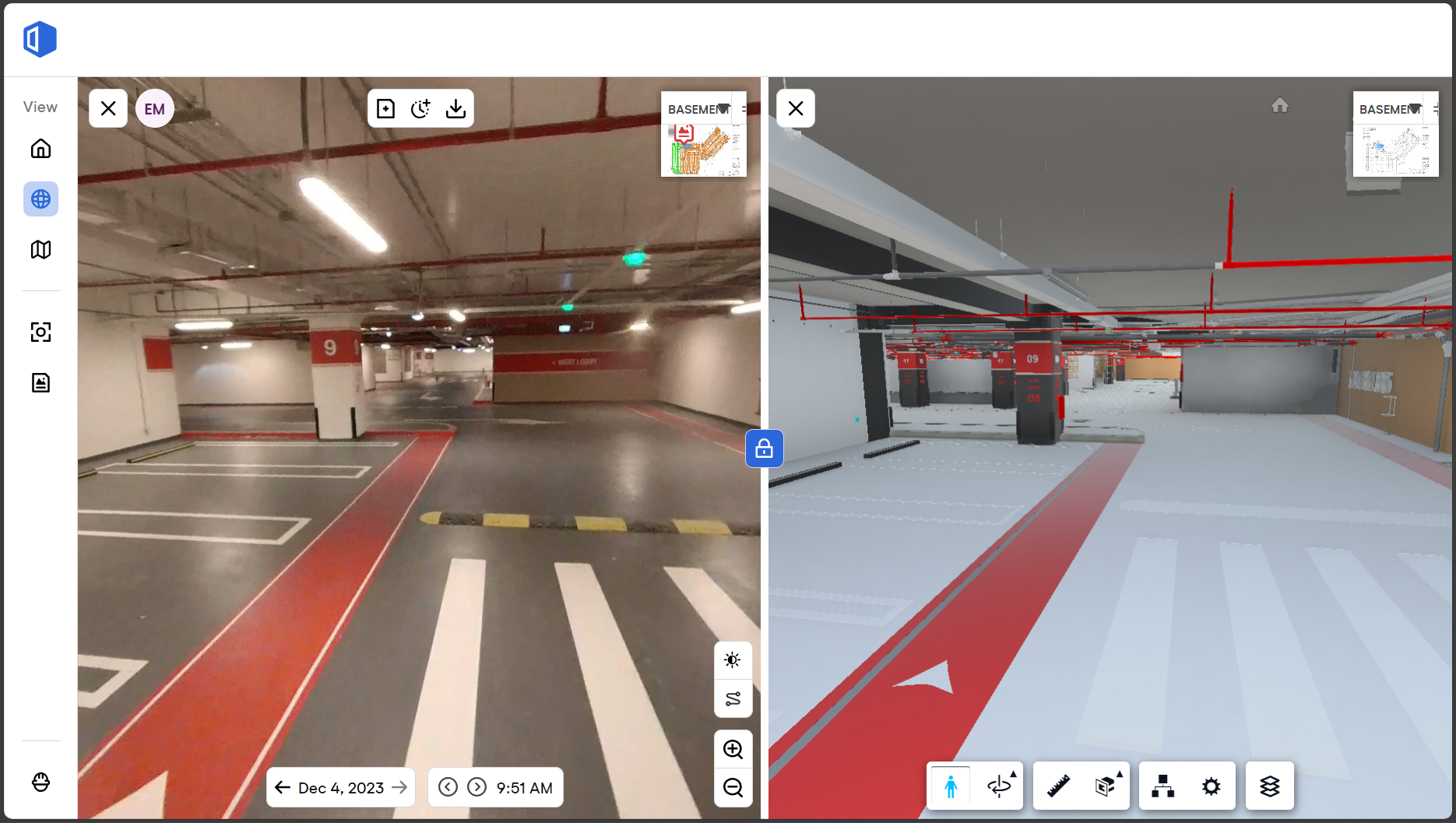
The results
Leveraging OpenSpace for 360° reality capture and site coordination enabled the team to quickly identify issues and bottle necks, monitor progress, verify work complete, and streamline team coordination. As a result, on December 27th 2023, the project successfully accommodated its first vehicle, in line with the initial project deadline. According to KEO, this proof of how OpenSpace can support large scale and complex projects also sets a new standard for future urban development projects, aligning with the Saudi Arabia “Vision 2030” pillars of economic diversification, social development and environmental sustainability.
Reduced site travel
With a complete digital visual record of the construction site at their fingertips, the project team was able to navigate the site remotely and in their own time. This way, OpenSpace helped to eliminate the need for physical inspections on-site, optimizing resource allocation and ultimately saving the team time and money.
Streamlined stakeholder management and coordination
Being able to refer to recent site captures when discussing specific issues or roadblocks allowed for clearer and faster communication and ultimately helped to achieve objectives faster. Whether it’s a quick question that needed clarification or a discussion around a larger issue “The compound effects provided significant overall results. Especially when it came to QA/QC close out.”, says Abdulmaqsud Hussein, Senior Project Manager at DGCL. Overall, the team handled and successfully closed over 8,000 QA/QC observations with the help of OpenSpace.
Accelerated project completion by 2 months
The time stamped 360° images pinned to the floor plan generated with OpenSpace provided the project team with all the proof they needed to compare site progress to the project schedule. This way it was easy to identify deviations from the schedule, and take corrective actions promptly or simply sign-off a project phase when everything was built to plan. As a result, the project stayed on track, and handovers were expedited.
More effective cost management
OpenSpace was used to facilitate quick verifications, particularly in critical areas such as Technical Rooms, where timely inspections were essential. This resulted in a much tighter control over the project budget, instilled confidence in stakeholders and ensured transparency in financial transactions.
Improved compliance and risk mitigation
Reports of project progress as well as health and safety behaviors were generated using OpenSpace captures as references, ensuring comprehensive documentation and visibility of potential risks. This incentivized the contractor to prioritize safety aspects, leading to improved HSE compliance and reduced risk exposure. Furthermore, potential failures or delays were identified early on, allowing for the team to react quickly and implement changes without destructive work needed.
Rolling out OpenSpace to 13 additional projects
Considering the successful implementation of OpenSpace in Historic Diriyah, along with the positive feedback from the client team and other stakeholders, this project has proven to be an effective Proof of Concept for further roll-out on additional projects. The successful pilot enables KEO to adopt Reality Capture technology as a crucial component of their Digital PMCM framework. To facilitate this transition, KEO has established an internal OpenSpace committee, a deployment plan, and several execution guides to support the roll-out of this technology to 13 additional projects across the GCC region.